
Out of all the activities that a person could do in their garage or backyard, few are as tool-intensive as woodworking. At auto shops, pressing plants and other settings in which complex arsenals of air-powered machinery are utilized, the higher capacity dual-stage units are the more preferable option. For the independent craftsperson, a single-stage compressor will power a variety of handheld pneumatic tools that don’t exceed 100 psi. However, two-stage compressors also cost more, which makes them better suited for factories and workshops than private use. Uses of Single-Stage vs. Dual-Stage Air Compressorsĭual-stage air compressors produce higher air power, which makes them a better option for large-scale operations and continuous applications. Single-stage air compressors are often small units that can easily be transported from one room to another. By contrast, multi-stage compressors are typically larger and somewhat heavier. On a single-stage compressor, all cylinders will be the same size and have their own inlet valves. On the other hand, in two-stage compressors, there is only one inlet, and the second piston is shorter than the first, and the two are linked by a cooling tube, which brings the temperature of the air down before the second round of compression. You can tell how many stages your air compressor has based on the size of the cylinders and the number of air intakes.
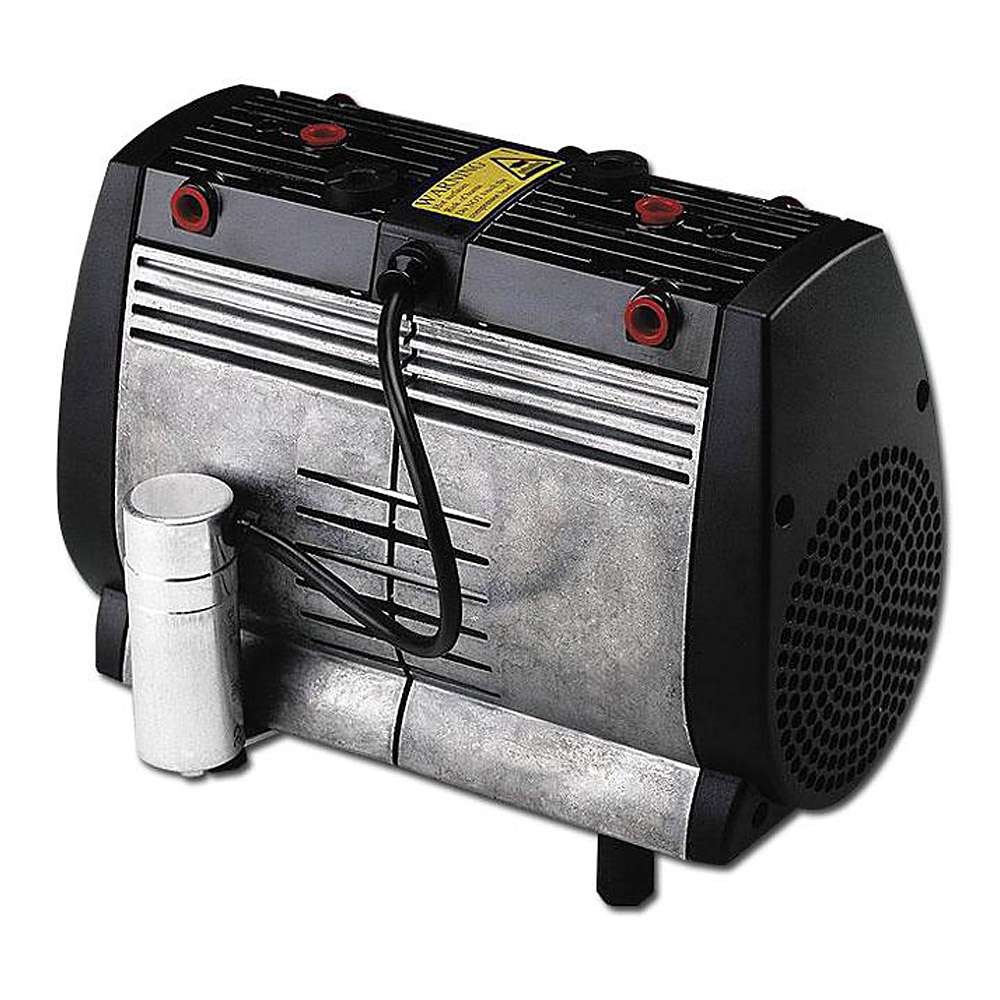
People who are new to air compressors will often confuse the number of cylinders for the number of stages in an air compressor, when in fact, both single- and two-stage compressors use two cylinders because it’s easier to balance air that way. From there, the double-pressurized air is cooled and delivered to a storage tank, where it serves as energy for vast arsenals of high-powered equipment. The process within a two-stage compressor - alternately referred to as a dual-stage compressor - is similar to that of a single-stage, but with one variation: the compressed air isn’t sent to a storage tank it’s instead sent to a smaller piston for a second stroke, this time at roughly 175 psi. In the storage tank, the compressed air serves as energy for the assortment of tools that a single-stage compressor is built to accommodate. The compressed air is moved onward to a storage tank.The trapped air is compressed in a single stroke with a piston at roughly 120 psi.The process that takes place within a single-stage compressor goes as follows:

Single-stage compressors are also known as piston compressors. In a single-stage compressor, the air is compressed one time in a two-stage compressor, the air is compressed twice for double the pressure.

The main difference between single- and two-stage compressors is the number of times that air gets compressed between the inlet valve and the tool nozzle.
